|
Motor |
Motor
Verbrennungsverfahren
|
siehe auch GDI | FSI |
HPI
| Common Rail |
Otto - Benzindirekteinspritzung
|
strahlgeführt
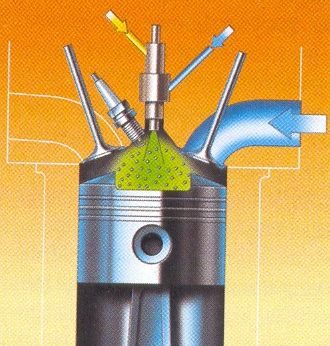
|
Kraftstoff wird (beim Ansaugen) in unmittelbarer Nähe der Zündkerze
eingespritzt und verdampft dort,
exakte Positionierung von Zündkerze und Einspritzdüse (vertikal) sowie
eine präzise Strahlausrichtung erforderlich, um das Gemisch zum richtigen
Zeitpunkt entzünden zu können, Zündkerze ist einer Wärmewechselbelastung
ausgesetzt, Einspritzdüsen meist mit Drallscheiben zur besseren
Verwirbelung, hohe Drücke von 200 bar;
strahlgeführte Brennverfahren werden als Zukunft bei der BDE
angesehen, es ist kein zerklüfteter Kolben (thermodynamische Probleme im
Homogenbetrieb) erforderlich wie bei wand- und luftgeführten Systemen,
in Erprobung
erwartet für 2006 bei BMW
System soll Leistung steigern und
Kraftstoffverbrauch senken |
wandgeführt
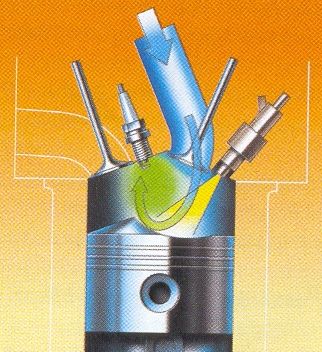
wandgeführt mit Tumble
wandgeführt mit Drall |
Allgemein:
Einspritzdüse seitlich, Zündkerze mittig, ausgeprägte Kolbenmulden (sog.
Nasenkolben)
Die Luft wird beim Ansaugen durch die Gestaltung von Einlasskanal und
Kolbenbodenform (Wand) in eine turbulente Strömung versetzt, je nach
Betriebszustand entweder im Ansaugtakt oder im Verdichtungstakt
eingespritzter Kraftstoff wird an Kolbenform umgelenkt, das
Kraftstoff-Luftgemisch gelangt als geschlossene zündfähige Wolke
entlang der Zylinderwand aber auch entlang dem Kolben zur Zündkerze, bei
Schichtladung nur kurze Zeitspanne vorhanden, Gemisch als geschichtete
Ladung ist spritsparend, funktioniert aber nur bei wenigen
Betriebszuständen, aufwändige Abgasnachbehandlung,
wandgeführt also deshalb, weil der Benzinstrahl durch Kolbenform und
Zylinderwand zur Zündkerze umgelenkt wird
Unterschied:
Ist die Rotationsbewegung mit horizontaler Achse wird der Begriff
walzenförmig
oder tumble
verwendet - Beispiel:
Mitsubishi
GDI
Ist
die Rotationsbewegung dagegen mit vertikaler Achse spricht man von
Drall
oder swirl
- Beispiel: Mercedes CGI
|
luftgeführt
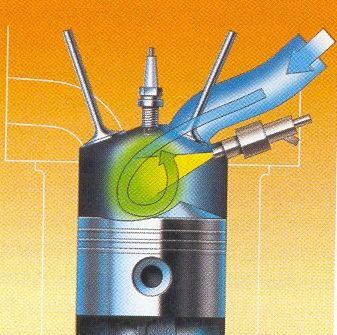
luftgeführt mit Walze |
Prinzipiell funktioniert dieses System wie bei den wandgeführten
Varianten.
Beim Ansaugen der Luft entsteht eine walzenförmige oder drallförmige
Luftströmung, die durch die Kolbenbodenmulde in Richtung Zündkerze
umgelenkt wird;
es erfolgt jedoch beim Einspritzen kaum eine Wandbenetzung, der in die
Luftströmung schräg eingespritzte Kraftstoff gelangt mit dieser Strömung
als geschlossene fette Wolke zur Zündkerze, die Kolbenform hilft hier mit
die Kolbenbodenmulde ist Strömungsmulde, der Kolben ist als Nasenkolben
ausgeführt, er dient zur Lenkung des Luftstroms, es entsteht weniger
HC als bei wandgeführtem System, Zeit zur Gemischaufbereitung ist noch
kürzer als bei wandgeführtem System
Der Unterschied zur wandgeführten Variante liegt darin, dass nur die Luft
vom Kolben umgelenkt wird und der Kraftstoff durch die Luftströmung zur
Zündkerze geführt wird
Beispiel:
FSI-Motoren von VW und AUDI
|
Diesel -
Diesel-Direkteinspritzung
|
luftverteilend
© Bosch
|
Kraftstoff wird durch eine Mehrlochdüse fein zerstäubt in die verdichtete
Luft eingespritzt, das Gemisch bildet sich in der Luft, es entsteht kaum
eine Wandbenetzung;
harter Lauf des Motors, Kaltstarthilfe nicht erforderlich,
in etwa gleichbedeutend wie die strahlgeführte Verbrennung beim Benzin-DI,
|
wandverteilend
|
Mittenkugel-Brennraum-Verfahren, MAN-M-Verfahren:
Angesaugte Luft wird in gewundenem Ansaugkanal in eine Drallbewegung
versetzt, der durch eine ein- oder Zweilochdüse, kaum zerstäubte,
eingespritzte Dieselkraftstoff bildet einen dünnen Kraftstofffilm auf der
kugelförmigen Kolbenmuldenwand, von der er schichtweise abdampft. Dies
führt zu einer weichen Verbrennung und einem ruhigen Lauf. Der Motor
ist als Vielstoffmotor einsetzbar. Der Kolben muss durch einen
Ölstrahl gekühlt werden. Das Abgasverhalten ist schlecht.
|
Diesel - Indirekte Einspritzung
(Geteilte Brennräume)
|
|
Frühere Mercedes-Diesel
Etwa ein Drittel des Verdichtungsraumes wird von der Vorkammer gebildet,
Kraftstoff wird mittels Zapfendüse in die Vorkammer gespritzt, Kraftstoff
verbrennt nur teilweise, Flamme wird über Kanäle in den Hauptbrennraum
gedrückt, es entsteht eine
weiche Verbrennung, Glühkerzen erforderlich
(im Bild 1 = Einspritzdüse, 2 = Vorkammer,
3 = Glühstift) |
Wirbelkammer-Verfahren

|
Frühere Diesel-Motoren
Luft wird beim Verdichten fast vollständig über einen tangentialen
Verbindungskanal vom Zylinder in die kugelförmige Wirbelkammer verdrängt,
es entsteht ein starker Wirbel, in diesen Drall wird der Kraftstoff
eingespritzt, das brennende Kraftstoff-Luftgemisch strömt in den
Hauptbrennraum hinüber, Motor läuft etwas härter als Vorkammer-Motoren,
Glühkerze erforderlich
(im Bild 1 = Einspritzdüse, 2 =
Wirbelkammer, 3 = Glühstift) |
Aufgeladene Direkteinspritzmotoren
haben einen höheren Wirkungsgrad und arbeiten deshalb
wirtschaftlicher als Kammermotoren.
Sie haben
einen sehr kompakten Brennraum, der meist in den Kolbenboden verlegt
ist. Die gute
Durchwirbelung der Luft wird zum einen durch die Quetschspalten, die
um die Kolbenmulde vorhanden sind und durch den Drall in den
Einslasskanälen erreicht.
Der Kraftstoff wird bei diesem
Verfahren durch eine Lochdüse,
gegenüber Zapfendüsen bei Kammermotoren, im Brennraum
gleichmäßig verteilt.
Die Anzahl der Bohrungen reicht bis
zu 12 Bohrungen.
Vorteile:
-
Geringe Wärmeverluste, wegen geringer Brennraumoberfläche,
-
geringerer Kraftstoffverbrauch,
-
keine
Vorglühanlage zum Starten erforderlich.
-
hoher Einspritzdruck
ist Vorteil da hierdurch kleinere Tröpfchen erreicht werden und so
eine bessere Durchmischung stattfindet
-
mehrere (z.B. 9) weiche
Kraftstoffkeulen, die in den Brennraum eingespritzt werden - die
Gemischbildung ist dann relativ gut -
-
der rauhe Lauf ist heutzutage mit
Voreinspritzung kontrollierbar geworden (eine kleine Menge Diesel
wird voreingespritzt und ermöglich es so der Haupteinspritzmenge in
einen Hochdruckbereich mit ausreichend Wärme und laufender
Verbrennung einzudringen - der Dieselschlag durch die verzögerte
Kraftstoffumsetzung kann so vermieden werden
Nachteile:
Hoher Einspritzdruck erforderlich (ab 300 bar), schlechtere
Gemischbildung, rauer harter Lauf durch schnellere Verbrennung,
kraftstoffempfindlich.
Sie kommen daher in allen NKW zum Einsatz, heute
auch im PKW.
Die
Nebenkammermotoren eigneten sich infolge
des geringeren Motorgeräusches besser für
PKW bei denen der Fahrkomfort auch eine wesentliche Rolle spielte.
Ferner hatten sie
niedrigere Herstellungskosten und verursachten niedrigere
Schadstoffemissionen
(HC und NOx).
Aber wegen des Kraftstoffmehrverbrauches von ca. 15% durch
Ladungswechselverluste und durch die moderne Technik
wurden sie immer mehr durch Motoren mit direkter Einspritzung ersetzt.
Beide Versionen sind gegenüber dem
Ottomotor
besonders im Teillastbereich sparsamer
(keine Drosselklappe). Der Dieselmotor eignet sich hervorragend für
die
Abgasturboaufladung.
Diese erhöht beim Dieselmotor nicht nur die Leistungsausbeute und
verbessert somit den Wirkungsgrad, sondern vermindert zudem die
Schadstoffe im Abgas und
das Geräusch.
•
Außerdem ist der Dieselmotor zur Verbrennung von alternativen
Kraftstoffen z.B. Rapsöl
geeignet. Hierfür muss allerdings vom Hersteller eine Freigabe
vorhanden sein,
gegebenenfalls muss die Einspritzausrüstung umgerüstet werden.
|
Mit
HCCI zum sauberen Motor
Wachsende Verkehrsströme erfordern immer
strengere Abgasnormen: Berliner Forscher arbeiten an einem neuen
Brennverfahren, um die Dieselmotoren für Pkw noch sauberer zu machen. Ein
erster Prototyp des so genannten HCCI-Motors existiert bereits.
HCCI steht für Homogeneous Charge Compression
Ignition. "Darunter verstehen wir ein neues Verbrennungsverfahren,
bei dem der in den Brennraum eingespritzte Kraftstoff dort verdampft und
sich schon vor der Zündung weitgehend homogen mit der Verbrennungsluft
mischt", erläutert Helmut Pucher, Professor für Verbrennungskraftmaschinen
an der TU Berlin. "Dieses homogene Gemisch wird sodann über die
Verdichtung kontrolliert gezündet. Bisher erreicht der Kraftstoff im
Brennraum eines normalen Dieselmotors nicht überall die erforderliche
Durchmischung, um mit der Luft schadstoffarm zu verbrennen. Dadurch
entstehen an manchen Stellen im Brennraum sehr hohe
Verbrennungstemperaturen, bei denen sich die schädlichen Stickoxide
bilden." Im HCCI-Motor liegt die Verbrennungstemperatur deutlich niedriger
als im herkömmlichen Dieselmotor, der Spitzen von über 2000 Grad Celsius
erreichen kann. "Um den Verbrennungsprozess zu regeln, nutzen wir unter
anderem die Abgasrückführung", fügt Pucher hinzu. "Bei relativ geringer
Motorlast, wie sie im Stadtverkehr benötigt wird, werden die Werte für
Stickoxide deutlich gedrückt - bei gleichem Verbrauch wie ein normaler
Dieselmotor."
Der HCCI-Motor stellt erhöhte Anforderungen an die Sensorik und die
Motorsteuerung, denn die Verbrennung muss in jeder Phase des Motorbetriebs
optimal ablaufen. "Dazu brauchen wir neue Steuerkonzepte wie das so
genannte zylinderdruckbasierte Motormanagement", erklärt Pucher. "Unsere
Stärke ist es, die Prozesse im Motor in Echtzeit zu simulieren, um daraus
neue Regelkonzepte abzuleiten."
|
Die künftigen Abgas-Grenzwerte liegen für
Diesel-Motoren in den wichtigsten Fahrzeugmärkten bei nur noch zehn bis 20
Prozent der aktuellen Werte. Aus heutiger Sicht lässt sich abschätzen,
dass die angestrebte Partikelreduktion wohl mit Abgasfiltersystemen
erreichbar ist, die Stickoxid-Vorgaben (NOx) jedoch eine Verringerung der
Rohemission erfordern. Deshalb wird weltweit sehr intensiv an
verschiedenen, neuartigen Brennverfahren wie HCCI (Homogeneous Charge
Compression Ignition), HCLI (Homogeneous Charge Late Injection), HPLI
(Highly Premixed Late Injection), DCCS (Dilution Controlled Combustion
System) geforscht, die sich alle durch sehr niedrige NOx-Emissionen
auszeichnen.
Allen genannten Verfahren ist eines gemeinsam: Die Zündung erfolgt in
Abhängigkeit des aktuellen Gemischzustands. (Beru) |
Lesen Sie auch die Berichte zu
GDI
| FSI | HPI |
Common Rail |
Quellen: H. Kopany
(Bosch), LUI (zum Thema: Dieseldirekteinspritzung), auto-motor-sport , Beru,
TU-Berlin,
von Johannes Wiesinger
bearbeitet:
09.03.2023
 |
|